In today's fast-paced business world, finding ways to improve efficiency and quality is essential. Kaizen, a Japanese term meaning 'continuous improvement,' offers a powerful approach to achieving these goals. This blog will explore seven effective Kaizen techniques that can help you streamline processes, enhance productivity, and foster a culture of improvement in your organization.
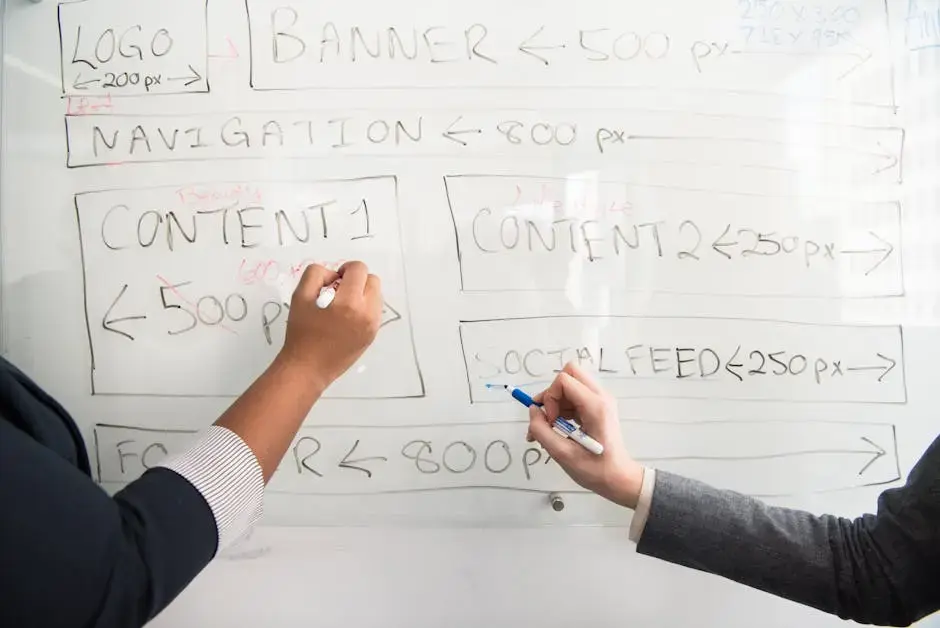
1. Empowering Employee Involvement
Engaging your workforce is pivotal in Kaizen. When employees are encouraged to share their ideas and insights, it leads to innovative solutions and a stronger commitment to improvement initiatives.
One effective way to promote this engagement is by establishing regular brainstorming sessions. These gatherings not only foster creativity but also deepen relationships among team members, leading to a more cohesive working environment. And when employees feel valued for their contributions, it can significantly boost morale.
Additionally, implementing suggestion boxes or digital platforms for anonymous feedback can further enhance employee involvement. This creates a safe space for individuals to voice their opinions without fear of judgment. Remember, fostering a culture of openness is essential!
2. Identifying and Eliminating Waste
One of the primary focuses of Kaizen is waste reduction. Learn how to identify areas where time, materials, or resources are wasted, and discover strategies to streamline those processes.
Waste can manifest in many forms—overproduction, waiting times, unnecessary transportation, and excess inventory, to name a few. Conducting a value stream mapping exercise can help visualize these inefficiencies, allowing you to pinpoint exactly where improvements can be made. This technique encourages a comprehensive examination of workflows from beginning to end.
Another effective strategy is the '5S' methodology: Sort, Set in order, Shine, Standardize, and Sustain. By organizing and standardizing your workspace, your team can minimize clutter and optimize efficiency. Once waste is identified and addressed, the positive impact on overall productivity will be unmistakable.
3. Implementing Standardized Work Processes
Creating standardized procedures can enhance efficiency and quality. We'll discuss how standardization helps reduce variations in performance and sets clear expectations for all team members.
Think of standard work processes as the backbone of your organization. They provide a consistent framework that everyone can rely on. Documentation is vital here; having clear instructions ensures that tasks are performed in the best way every time. This not only maintains quality but also makes training new employees smoother and quicker.
The beauty of standardization lies in its adaptability. As your business evolves, your processes can, too. Regularly revisiting these standards and involving team members in updates can help keep practices relevant and efficient. In essence, it sets your team up for success!
4. Encouraging Continuous Feedback Loops
Establishing a culture of feedback is essential in Kaizen. By promoting continuous communication, your team can quickly address issues and identify areas for improvement.
Think of feedback as a driving force for change. When team members feel comfortable sharing thoughts on processes and ideas, it opens doors to enhancements that might otherwise go unnoticed. Regular feedback sessions, whether weekly or monthly, ensure that everyone is on the same page and aligned with organizational goals.
Moreover, incorporating both positive and constructive feedback creates a balanced environment. Recognizing achievements reinforces good practices, while constructive discussions can guide the team toward improvements. Ultimately, this approach promotes a growth mindset, crucial for a successful Kaizen initiative.
5. Utilizing PDCA for Structured Improvement
The Plan-Do-Check-Act (PDCA) cycle is a cornerstone of Kaizen. This section will explore how to effectively implement PDCA in your organization to foster a structured approach to continuous improvement.
Beginning with the 'Plan' phase, it’s important to set clear objectives. This part involves data collection and analysis to identify improvement opportunities. Once you have a solid plan, proceed to the 'Do' phase, implementing the changes on a small scale or as a pilot project.
Following that, during the 'Check' phase, it’s vital to evaluate the results obtained from practices. Analyze what worked, what didn’t, and why. Finally, the 'Act' phase allows for making adjustments based on findings to ensure the most effective practices are standardized and implemented broadly. This cyclical process ensures that continuous improvement becomes an inherent aspect of your organizational culture.
6. Integrating Visual Management Tools
Visual management tools can significantly enhance understanding within teams. Learn about various tools that can help visualize performance metrics and progress towards improvement goals.
The use of Kanban boards is a popular choice in many organizations. These boards provide a clear roadmap, allowing teams to see workflows and task statuses at a glance. It promotes accountability and collaboration, as everyone in the team can track progress together, fostering a shared sense of purpose.
Additionally, scorecards displaying key performance indicators (KPIs) can keep all members informed and motivated. The visibility of these metrics serves to align efforts and focus improvements where they're needed most. Putting this into practice not only keeps everyone engaged but also encourages a proactive approach to problem-solving.
7. Building a Culture of Continuous Improvement
Ultimately, Kaizen is as much about culture as it is about process. We'll discuss strategies for cultivating an organizational mindset focused on ongoing improvement and growth.
Creating an environment where continuous improvement is valued takes commitment. Leadership plays a crucial role in modeling this mindset; when leaders demonstrate a passion for Kaizen, it inspires the entire team to embrace the same values. Regular training sessions that highlight Kaizen principles also reinforce the importance of these practices.
Moreover, celebrating small wins can create a positive feedback loop, motivating everyone to pursue improvement relentlessly. Encouraging sharing of success stories, whether big or small, can fuel enthusiasm for ongoing efforts. Remember, a collaborative culture rooted in Kaizen principles empowers everyone to contribute to the organization’s success.
Commentaires