In today's fast-paced business world, efficiency is more crucial than ever. Lean and continuous improvement methodologies offer powerful strategies to streamline processes, reduce waste, and enhance productivity. This blog will explore how these approaches can help organizations achieve better results.
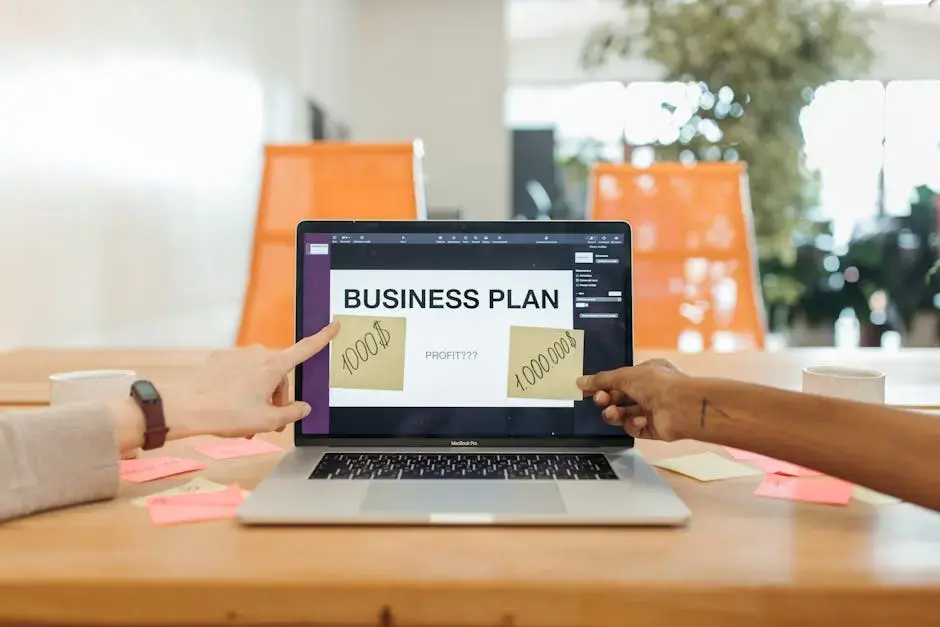
Understanding Lean Principles
Lean principles focus on minimizing waste while maximizing value. It's essential to grasp these concepts to enhance efficiency.
At its core, lean is all about creating more value for customers with fewer resources. This means examining every step in your process and removing anything that doesn't add value.
A crucial tenet of lean thinking is understanding the value stream. By mapping out how value flows through your organization, you can pinpoint areas where waste occurs, helping your team become more efficient.
Moreover, lean principles encourage a culture of collaboration and open communication. When employees understand their roles in reducing waste, they're empowered to contribute to the organization's efficiency.
Exploring Continuous Improvement
Continuous improvement, or Kaizen, involves regularly analyzing and refining processes to increase efficiency. Discover how this practice can transform your approach.
By fostering a mindset of continuous improvement, organizations encourage employees at all levels to suggest changes, no matter how small. This creates a ripple effect, leading to significant efficiency gains over time.
Central to continuous improvement is feedback. By continuously assessing performance through metrics and employee insights, businesses can adapt processes swiftly, ensuring they remain competitive in their industry.
Furthermore, the cycle of plan-do-check-act (PDCA) inherent in continuous improvement helps teams systematically address issues. This structured approach means that improvements can be both incremental and sustainable.
Identifying Areas for Improvement
Knowing where to focus your efforts is key. Learn how to identify bottlenecks and areas that require enhancement.
The first step in identifying areas for improvement often involves conducting a thorough analysis of your current processes. Utilize tools like value stream mapping to visualize where inefficiencies lie.
Employee input is invaluable in this phase. Regular discussions and feedback sessions can help uncover pain points that may not be immediately visible in data analysis.
Additionally, benchmarking against industry standards can provide a clearer picture of where you stand. By understanding how leading organizations operate, you can set realistic and achievable goals for improvement.
Implementing Lean Strategies
Explore effective strategies to implement lean practices in your organization. Practical tips will guide you through the process.
Begin by securing buy-in from all levels of the organization. When leadership exhibits commitment to lean principles, it sets a positive tone that encourages wider acceptance.
Training is critical. Ensuring that employees are well-versed in lean methodologies will allow them to contribute meaningfully to the organization's efficiency efforts.
Another important strategy is to start small. Implementing lean practices in isolated areas can provide insights and successes that can then be scaled organization-wide.
Remember, ongoing communication is vital during this transition. Regular check-ins can help keep everyone aligned and motivated on the continuous improvement journey.
Measuring Success
Finally, it's important to measure the effectiveness of your lean and continuous improvement efforts. Learn how to utilize key performance indicators to track progress.
Setting clear, measurable objectives allows organizations to assess whether their lean initiatives are achieving desired outcomes. KPIs should align with both corporate goals and lean principles.
Also, don't forget the qualitative aspects of measurement. Employee satisfaction, customer feedback, and process efficiency all provide valuable insights into the effectiveness of your initiatives.
In conclusion, measuring success isn't a one-time event but an ongoing process. Regularly reviewing performance data ensures that your team remains agile, ready to adapt and improve over time.
Final Thoughts on Lean and Continuous Improvement
By embracing lean principles and committing to continuous improvement, organizations can create a culture of efficiency that drives success. These methodologies not only improve processes but also foster innovation and adaptability, essential traits in a competitive landscape.
Comments